Understand the Differences Between Lean Certification Levels
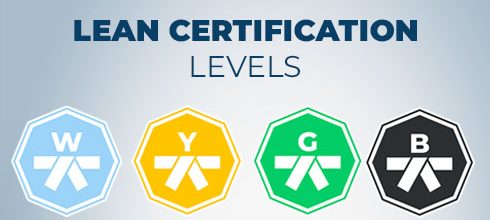
In this article, we will explore the differences between Lean certifications: White Belt, Yellow Belt, Green Belt, and Black Belt. What are the differences? How are they structured? How can you become certified? That’s what we will explain.
You can also listen to Julien Charles, CEO of 7-Shapes, talk about it: https://www.youtube.com/watch?v=HWhI6kZ-TAo (in French).
AFNOR NFX 06-091 STANDARD: A FRAMEWORK FOR CERTIFICATIONS
In France, the AFNOR NFX 06-091 standard details the required skills for each Lean certification level: Yellow, Green, and Black Belt. This standard, in application since 2011 and currently under revision, distinguishes two main aspects: technical skills (Lean tools and methods) and soft skills (change management, leadership, communication).
LEAN TOOLS: SIX CATEGORIES
Lean tools are divided into six categories, ranging from the simplest to the most complex:
- Basic Tools: Causal Analysis (Ishikawa), 5 Whys, brainstorming, VSM (Value Stream Mapping), OEE (Overall Equipment Effectiveness), red/green analysis, spaghetti flow.
- Standardized Work: Process analysis, capability sheets, kitting (logistics kit preparation).
- Autonomation (Jidoka): Poka-yoke, andons, autonomous maintenance (TPM).
- Visual Management: 5S, short-interval management, production standards.
- Pull Systems: Kanban, supermarkets, Milkman system, ABC analysis.
- Production Leveling (Heijunka Box): SMED, batch size calculations, etc.
Lost among all these acronyms? Check out our glossary.
LEAN CERTIFICATION LEVELS
Lean certification levels are structured like a pyramid, with each level bringing increased skills and responsibilities:
White Belt: This level provides a general overview of Lean, with basic knowledge of Lean history, the Lean house, types of waste, and some problem-solving tools (5S, simple methodologies). It’s a short training aimed at familiarizing the entire company with Lean principles.
Know more about White Belt training
Yellow Belt: Yellow Belts can solve local problems at their workstation using basic Lean tools and standardized work techniques. They assist White Belts and lead small problem-solving projects following the PDCA (Plan-Do-Check-Act) cycle.
Know more about Yellow Belt Training
Green Belt: Green Belts lead more complex projects that cover multiple workstations or a production line. They use tools from the first four categories (basic tools, standardized work, autonomation, visual management). They manage budgets, schedules, and teams, and their projects are often fueled by maps created by Black Belts.
Know more about Green Belt training
Black Belt: Black Belts supervise multiple Green Belt projects, manage strategic initiatives, and use advanced tools (pull systems, production leveling). Their scope is broad, covering the entire value chain of an industrial site, including related aspects like logistics and information systems.
Know more about Black Belt training
Practice : The Key to Success
Mastering Lean requires more than just studying theories and tools: practice is essential. Whether through case studies or real projects, it is crucial to develop skills in leadership and change management.
A well-structured training plan, supported by concrete projects, helps build a solid foundation of knowledge and skills within the company.
Conclusion
There is a detailed guide to help you identify the skills and tools required at each Lean certification level. A new version of the AFNOR NFX 06-091 standard, focused on skills development, will be released soon.
Depending on your sector, constraints, and goals, it is ideal to train:
- 100% of your teams at the White Belt level
- 50% at the Yellow Belt level
- 10-15% at the Green Belt level
- 2-3% at the Black Belt level.
Our last posts
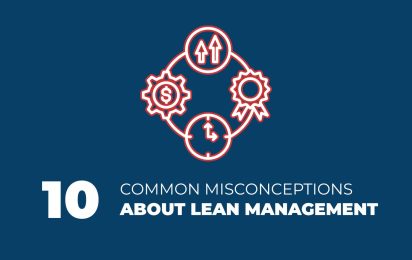
10 Common misconceptions about lean management
10 Common misconceptions about lean management Lean Management- sound familiar? This organizational approach, renowned for transforming companies into well-oiled machines,…
Lire l’article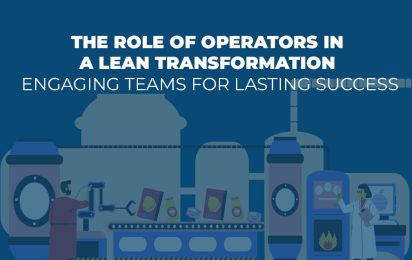
The Role of Operators in a Lean Transformation: Engaging Teams for Lasting Success
How can businesses stay competitive in an ever-evolving world? How can they eliminate waste while creating more value every day?…
Lire l’article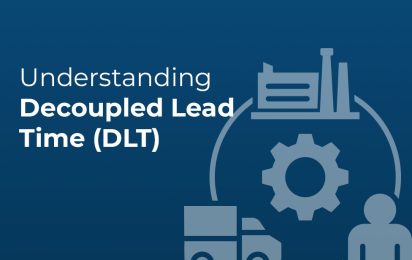
Decoupled Lead Time (DLT): Understanding and Optimizing Lead Time in Supply Chains
In a context where responsiveness and flexibility have become essential, companies are constantly seeking to optimize their supply chains. Among…
Lire l’article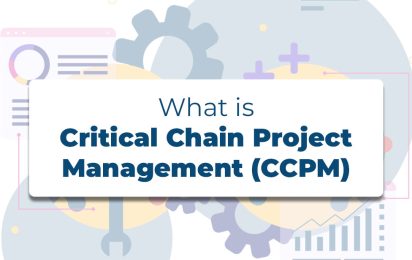
Critical Chain Project Management (CCPM)
In this article, we will explain how to balance a production line to optimally meet customer demand. You will find…
Lire l’article