WHAT IS THE KANBAN METHOD AND HOW TO APPLY IT?
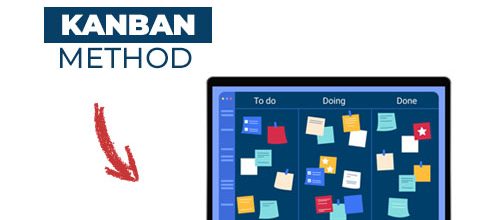
In this article, we will explore the various aspects of the Kanban method, including its basic principles, the types of Kanban flows, and the advantages of a pull system over a push system.
We will also cover essential concepts such as the Kanban supermarket, calculating the Kanban loop, and the different Kanban stock zones.
WHAT IS THE KANBAN METHOD?
The Kanban method originated in Japan with the Toyota Production System. The term “Kanban” means tag or signal in Japanese and allows for the simple and visual management of workflow and work-in-progress. This method was created in the 1950s by Taiichi Ohno, one of the pioneers of the Toyota Production System.
THE BASIC PRINCIPLES OF KANBAN
Kanban aims to manage work-in-progress in a way that avoids overproduction and excess inventory. It allows the production flow to adapt to the actual demand of customers. One of the goals of Kanban is to make inventory visible and controllable, while empowering field operators rather than centralizing all decisions in an ERP (Enterprise Resource Planning) system.
TYPES OF KANBAN FLOWS
There are mainly two types of Kanban flows:
- Production Kanban: Between two stages of production.
- Logistics Kanban: Between a production stage and the warehouse that delivers components or raw materials.
PUSH vs PULL FLOWS
- Push Flow : In a push flow, production is dictated by a centralized plan without considering real-time demand fluctuations. This can lead to excess inventory and overproduction.
- Pull Flow : In a pull flow, each production stage starts only when demand is generated by the next downstream stage. This creates a more responsive system aligned with actual demand, limiting excess inventory.
KANBAN SUPERMARKET
A Kanban supermarket is an intermediate storage area that maintains a limited stock of parts or raw materials. When a part is removed, a signal is sent to produce or deliver a new part. This helps maintain a balance between demand and production.
CALCULATING THE KANBAN LOOP
To implement an effective Kanban system, it is essential to correctly calculate the Kanban loop, which determines the necessary stock to meet demand while minimizing excess.
KANBAN STOCK ZONE
- Red Zone: Minimum stock necessary to avoid shortages.
- Yellow Zone: Safety stock to absorb demand fluctuations.
- Green Zone: Stock quantity aligned with production lot sizes.
CONCLUSION
The Kanban method is a powerful tool for improving production efficiency by making workflows visible and reducing waste. It allows for more precise responses to customer demand while limiting excess inventory.
We hope this introduction to the Kanban method has been helpful. Do you have any questions or would you like to explore the topic further? Contact us.
OUR LAST POSTS
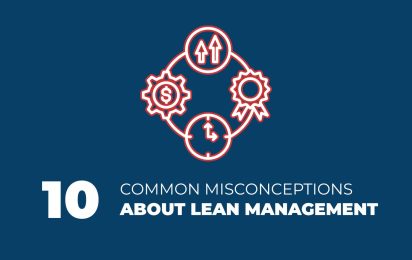
10 Common misconceptions about lean management
10 Common misconceptions about lean management Lean Management- sound familiar? This organizational approach, renowned for transforming companies into well-oiled machines,…
Lire l’article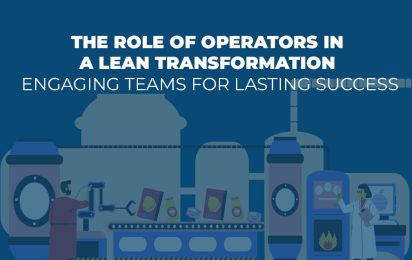
The Role of Operators in a Lean Transformation: Engaging Teams for Lasting Success
How can businesses stay competitive in an ever-evolving world? How can they eliminate waste while creating more value every day?…
Lire l’article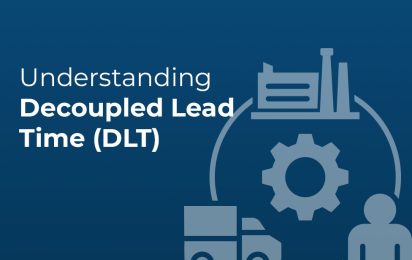
Decoupled Lead Time (DLT): Understanding and Optimizing Lead Time in Supply Chains
In a context where responsiveness and flexibility have become essential, companies are constantly seeking to optimize their supply chains. Among…
Lire l’article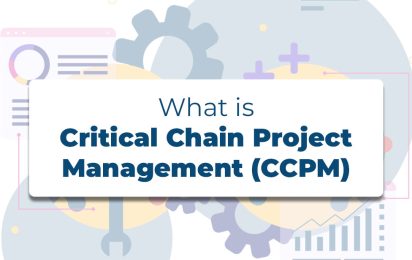
Critical Chain Project Management (CCPM)
In this article, we will explain how to balance a production line to optimally meet customer demand. You will find…
Lire l’article