The Role of Operators in a Lean Transformation: Engaging Teams for Lasting Success

How can businesses stay competitive in an ever-evolving world? How can they eliminate waste while creating more value every day? Lean transformation provides powerful answers to these challenges, but one critical question remains: who truly drives this transformation? Tools and processes alone are not enough. The real strength of Lean lies in the operators—those field experts who understand the inner workings of the company better than anyone else. How can we fully engage them to turn a Lean initiative into lasting success?
Understanding Lean Transformation
Lean is built on two fundamental pillars: continuous improvement and respect for people. Its goal is to eliminate waste to increase added value while involving teams at every level of the organization. While executives and managers play a strategic role, operators are the ones who implement changes daily.
Why Operators Are Essential
Operators possess practical, hands-on knowledge of processes. They interact daily with tools, machines, and products, enabling them to spot inefficiencies or anomalies that managers may overlook. Their expertise is crucial for:
- Identifying waste: Operators are often the first to notice wasted time, effort, or resources.
- Proposing practical solutions: Their ideas are typically pragmatic and grounded in the realities of the workplace.
- Testing improvements: Their mastery of tasks allows them to quickly validate adjustments.
Engaging Operators: A Key to Success
Successfully implementing Lean transformation requires actively engaging operators. Here’s how their involvement can be encouraged:
1. Giving Meaning to the Change
Teams need to understand why the Lean transformation is being implemented and how it will benefit them. Clear and transparent communication is essential, explaining how these initiatives will not only enhance the company’s performance but also improve their working conditions.
2. Encouraging Active Participation
Operators should not merely execute decisions made by leadership. Instead, they should be treated as partners. Lean tools such as Kaizen workshops, quality circles, and suggestion boards foster participation by encouraging teams to share their ideas.
3. Training and Equipping Teams
Learning is key to transformation. Training operators in Lean tools and principles (such as 5S, Just-In-Time, or Kanban) equips them with the skills to identify and solve problems. This also empowers them and strengthens their sense of belonging.
4. Recognizing Contributions
Recognition is a powerful motivator. Celebrating successes, whether it’s a minor improvement or a major breakthrough, demonstrates that operators’ efforts are appreciated and encourages further initiatives.
The Role of Managers in Engaging Operators
Managers play the role of facilitators, creating an environment that fosters engagement. They must actively listen, provide constructive feedback, and act as mentors. Additionally, they need to ensure that operators have the time and resources to fully invest in Lean initiatives.
The Benefits of Sustainable Engagement
When operators are actively involved in Lean transformation, the benefits are significant:
- Continuous improvement: Solutions arise directly from the needs and observations of the field.
- Greater acceptance of change: Teams involved from the outset feel more committed to new practices.
- Skill development: Operators gain problem-solving and collaborative skills.
- A culture of operational excellence: Over time, continuous improvement becomes second nature, embedding Lean into the company’s DNA.
Conclusion
In a Lean transformation, operators are not merely cogs in a well-oiled machine—they are critical actors in its success. Their engagement ensures not only the effectiveness of Lean initiatives but also their sustainability.
By recognizing their role, providing training, and valuing their contributions, companies can ensure that Lean is not a passing trend but a deeply rooted philosophy, driven by the talent and creativity of those working at the heart of their processes.
Adopting an operator-centric approach optimizes performance while enhancing team satisfaction and motivation, paving the way for lasting success.
last blog posts
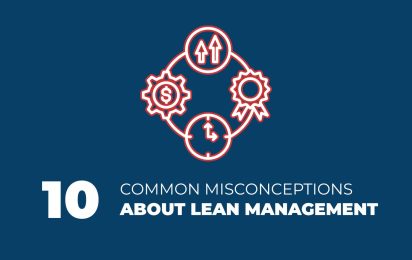
10 Common misconceptions about lean management
10 Common misconceptions about lean management Lean Management- sound familiar? This organizational approach, renowned for transforming companies into well-oiled machines,…
Lire l’article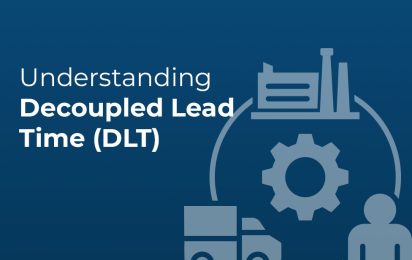
Decoupled Lead Time (DLT): Understanding and Optimizing Lead Time in Supply Chains
In a context where responsiveness and flexibility have become essential, companies are constantly seeking to optimize their supply chains. Among…
Lire l’article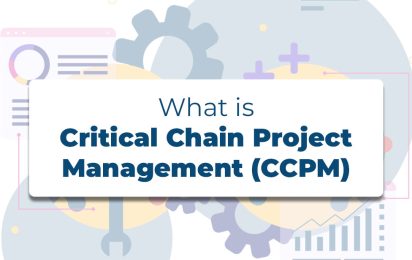
Critical Chain Project Management (CCPM)
In this article, we will explain how to balance a production line to optimally meet customer demand. You will find…
Lire l’article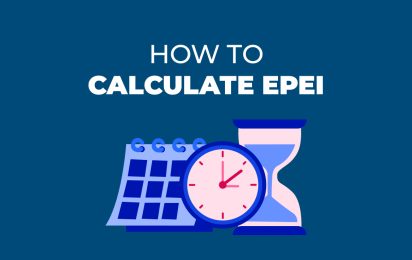
What is EPEI and how to calculate it?
In the world of Lean manufacturing and industrial process management, Every Part Every Interval (EPEI) is a fundamental concept for…
Lire l’article