Optimizing Processes with the Queue Management System
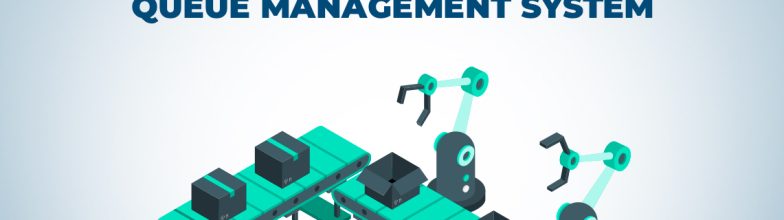
In today’s world, where competition and the pursuit of profit are more intense than ever, every company is striving to maximize efficiency while minimizing waste. Lean Management, which focuses on creating value by eliminating waste, offers a variety of tools and techniques to achieve this. Among these tools, the queue management tool stands out as a valuable asset. Curious to learn more? You’re in the right place!
What is the Queue Management System?
The queue management tool, or simply a queue, refers to a group of individuals waiting in an organized manner for something. Queues result from demand exceeding the capacity to deliver a product or service.
This method is used to manage and optimize workflows by analyzing points where processes can be slowed down or blocked by queues. By identifying these congestion points, companies can take action to improve the flow and speed of their operations.
Why Do Queues Form?
Queues often form for several reasons:
- Insufficient Capacity: When demand exceeds available capacity, queues naturally form.
- Demand Variability: Unpredictable fluctuations in demand can lead to queues if resources cannot adapt quickly.
- Inefficient Processes: Poorly designed or inefficient processes can create bottlenecks and delays.
The Benefits of Using the Queue Management Tool
Applying the queue management tool within a Lean Management strategy offers several benefits:
- Reducing Wait TimesBy analyzing and optimizing queues, companies can reduce wait times for customers, thereby improving customer satisfaction and operational efficiency.
- Improving ProductivityIdentifying and reducing bottlenecks helps speed up production processes and increases overall productivity.
- Better Resource AllocationThe queue management tool helps better understand where and when resources are needed, allowing for more efficient allocation and avoiding overuse or underutilization.
- Increased FlexibilityWith more effective workflow management, companies can better respond to demand variations and adjust their operations accordingly.
How to Implement the Queue Management Tool
- Map the ProcessesThe first step is to map out existing processes to identify where queues are forming. This can be done using process flow diagrams or value stream maps.
- Measure Wait Times and CapacitiesCollect data on wait times and the capacities of each process step. This will provide a clear view of congestion points.
- Analyze the DataUse analytical tools to identify the causes of queues. This may include statistical analyses, simulations, or modeling approaches.
- Develop SolutionsPropose and implement solutions to reduce or eliminate queues. This may involve adjusting capacities, reengineering processes, or adding additional resources.
- Monitor and AdjustFinally, continuously monitor the processes to ensure the implemented solutions are effective and make adjustments as needed.
Case Study: Improving a Production Line
Let’s take the example of a drone assembly plant. By applying the queue management tool, the plant mapped out its processes and identified several bottlenecks during the final assembly of the drones. After analysis, they discovered that the capacity of certain machines was insufficient relative to the growing demand.
To address this issue, the plant invested in additional machines and trained operators to maximize efficiency. As a result, wait times were reduced by 40%, and productivity increased by 25%. This optimization not only improved the smoothness of operations but also allowed the plant to respond more quickly to orders, thereby increasing customer satisfaction.
Conclusion
The queue management tool is an essential component of Lean Management, enabling companies to effectively manage their workflows and minimize waste. By identifying and eliminating bottlenecks, organizations can enhance their efficiency, productivity, and customer satisfaction. Integrating this methodology into your Lean strategy can yield significant and sustainable results.
Our last posts
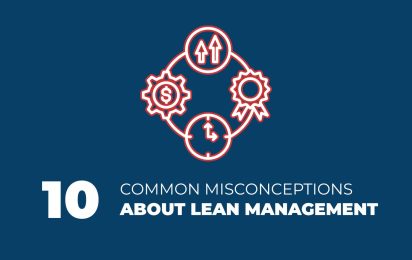
10 Common misconceptions about lean management
10 Common misconceptions about lean management Lean Management- sound familiar? This organizational approach, renowned for transforming companies into well-oiled machines,…
Lire l’article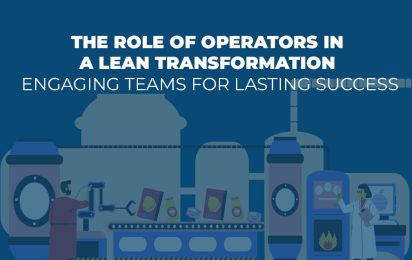
The Role of Operators in a Lean Transformation: Engaging Teams for Lasting Success
How can businesses stay competitive in an ever-evolving world? How can they eliminate waste while creating more value every day?…
Lire l’article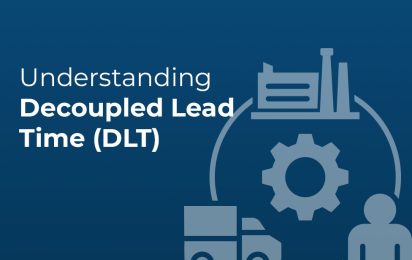
Decoupled Lead Time (DLT): Understanding and Optimizing Lead Time in Supply Chains
In a context where responsiveness and flexibility have become essential, companies are constantly seeking to optimize their supply chains. Among…
Lire l’article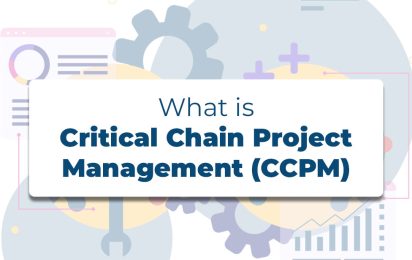
Critical Chain Project Management (CCPM)
In this article, we will explain how to balance a production line to optimally meet customer demand. You will find…
Lire l’article