Decoupled Lead Time (DLT): Understanding and Optimizing Lead Time in Supply Chains
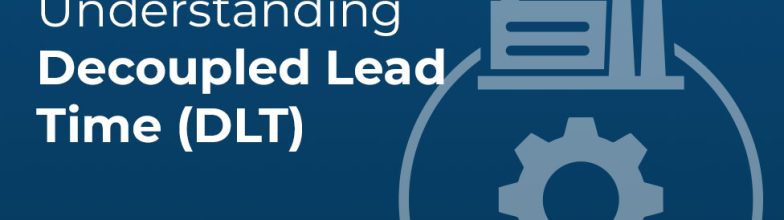
In a context where responsiveness and flexibility have become essential, companies are constantly seeking to optimize their supply chains. Among the many strategies, the concept of Decoupled Lead Time (DLT) has gained popularity for its ability to reduce response times and improve inventory management.
But what is DLT, and how can it benefit your company? In this article, we will explore this concept in detail and examine how it can be implemented to make your supply chain more efficient.
What is Decoupled Lead Time (DLT)?
Decoupled Lead Time (DLT) is an inventory and production flow management method that separates production from demand. In other words, it involves decoupling the production of finished products from customer demand through a decoupling point, often situated at the level of semi-finished products or raw materials inventory.
This separation allows faster responses to demand while maintaining stable and efficient production. Instead of producing to meet each individual customer order, the company produces components or sub-assemblies that can be quickly assembled to fulfill specific orders, thereby reducing delivery times.
Why Use DLT?
- Reduced Delivery Times: DLT shortens delivery times by reducing the period between the customer order and the delivery of the final product. Companies can store sub-assemblies or components, ready to be assembled quickly according to customer needs.
- Inventory Optimization: By separating production processes from demand, companies can maintain optimized inventory levels, avoiding overstock and stockouts. This reduces storage and waste-related costs.
- Improved Flexibility: DLT offers greater flexibility, enabling companies to respond to demand fluctuations without continually adjusting production. This translates into better capacity for handling customized products or special orders.
- More Efficient Planning: Thanks to decoupling, companies can plan their production based on long-term demand forecasts rather than reacting to each individual order, reducing stress on the production chain.
How Does Decoupled Lead Time Work?
The DLT principle relies on establishing a decoupling point that acts as a buffer between production flows and customer orders. This decoupling point can be placed at different levels of the production chain, depending on product types and the company’s needs:
- Raw materials stock: Raw materials are stored and ready to be transformed based on orders.
- Semi-finished products stock: Sub-assemblies or components are produced in advance and stored. When an order is received, these components can be quickly assembled.
- Finished products stock: Finished products are stored for immediate delivery, used for products with predictable and stable demand.
- Implementing DLT: Key Steps
- Supply Chain Analysis: Identify key production processes and material flows. Understand where bottlenecks occur and how demand fluctuates.
- Determine Optimal Decoupling Point: Choose the most strategic location for your decoupling point based on inventory levels, production times, and customer needs.
- Stock Planning: Calculate the necessary stock levels to ensure that components or sub-assemblies are available for quick production, while avoiding unnecessary stock excess.
- Monitoring and Adjustment: Use key performance indicators (KPIs) to track DLT effectiveness and adjust stock levels and the position of the decoupling point based on changing demand trends.
Practical Cases: Examples of DLT Usage
- Automotive Industry: Automotive manufacturers often use DLT by producing standard components (like engines or chassis) and storing them until specific orders are received. This enables them to customize vehicles according to client preferences without delaying overall production.
- Consumer Electronics: Companies manufacturing electronics, such as smartphones or computers, use DLT to produce standard components in large quantities, which are then quickly assembled into finished products per customer specifications.
Advantages and Limitations of DLT
Advantages:
- Reduction in production and delivery times.
- Improved production flexibility.
- Reduced inventory-related costs.
- Better management of demand variability.
Limitations:
- High initial investment: Implementing a DLT system requires investments for inventory management and planning.
- Increased complexity: Managing decoupled inventory can be complex, especially for highly diverse or customized products.
Conclusion
Decoupled Lead Time (DLT) represents a strategic approach for companies looking to optimize their supply chains by reducing delivery times and increasing production flexibility. By decoupling production from demand, this method offers better inventory management, greater responsiveness to customer orders, and significant cost reductions. However, implementing it requires careful planning and a thorough understanding of the company’s supply chain.
Our last posts
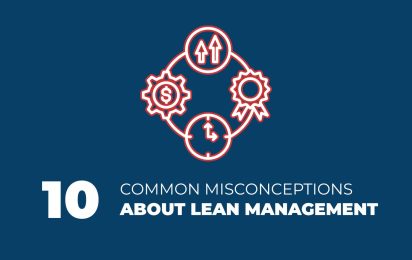
10 Common misconceptions about lean management
10 Common misconceptions about lean management Lean Management- sound familiar? This organizational approach, renowned for transforming companies into well-oiled machines,…
Lire l’article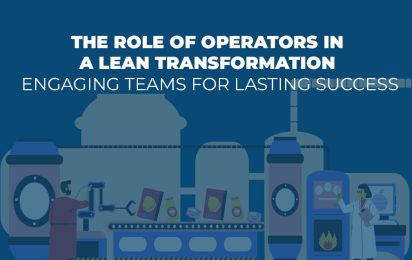
The Role of Operators in a Lean Transformation: Engaging Teams for Lasting Success
How can businesses stay competitive in an ever-evolving world? How can they eliminate waste while creating more value every day?…
Lire l’article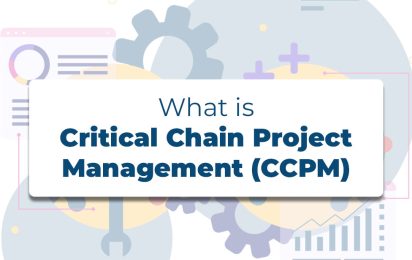
Critical Chain Project Management (CCPM)
In this article, we will explain how to balance a production line to optimally meet customer demand. You will find…
Lire l’article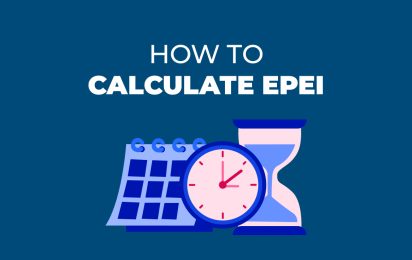
What is EPEI and how to calculate it?
In the world of Lean manufacturing and industrial process management, Every Part Every Interval (EPEI) is a fundamental concept for…
Lire l’article