Critical Chain Project Management (CCPM): The approach to managing your projects in a multi-project environment.
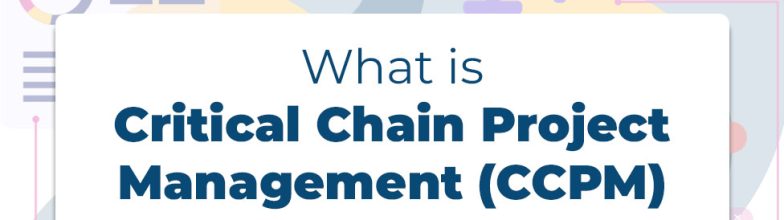
In this article, we will explain how to balance a production line to optimally meet customer demand. You will find here the key concepts to master, as well as the calculations you need to apply.
Line Balancing: What Are We Talking About?
Balancing a production line involves organizing the right number of steps necessary to achieve the desired volume from the customer. In other words, it is about distributing the work so that each production station can operate smoothly and without interruption.
We will discuss Takt time, the analysis of red and green times, and the calculations you need to master to adjust your production line, whether you are developing a new product or improving an existing line.
Understanding Red and Green Times
The first step in balancing your production line is to distinguish between green, orange, and red times.
- Green Times: These are value-added times, meaning the time you actually spend producing and transforming your product.
- Orange Times: These are non-value-added but essential times. For example, quality control times or mandatory movements in the process that you cannot eliminate immediately but that remain necessary in the short term.
- Red Times: Here, it is essential to make an important distinction. Red times refer to non-value-added times that you ideally should eliminate. However, these are often short-term unavoidable red times that you cannot remove immediately (for example, technical problems, process defects, or delays related to inefficiencies). Even though these times should be targeted for future improvements, they are not used to rebalance a production line.
It is crucial to note that to rebalance a line, you should primarily work on reducing red times in the long term, but they should not be integrated as fixed parameters in the balancing. Instead, they serve as axes for future improvement.
Let’s take the example of industrializing a new product. To define a production line, the first step is to add up the green times, then add the orange and red times. This will give you the total time required to manufacture your product.
The Importance of Takt Time
The second crucial concept for line balancing is Takt time. Takt time represents the pace at which you need to produce a finished product to meet customer demand. To calculate it, you need to divide your daily operating time by customer demand.
Let’s take a concrete example: suppose your company operates for 7 hours a day and you have a demand for 70 products to deliver. The Takt time will then be 6 minutes per product (420 minutes of production / 70 products). This means that one product must be completed every 6 minutes to keep up with demand.
Balancing the Line: An Essential Calculation
With the Takt time and green and red times calculated, you can now determine the ideal number of steps on your production line. Simply divide the total time required to produce one product (green time + orange time + red time) by the Takt time. This calculation will tell you how many steps are necessary for each product to be completed on time.
Assuming your current line takes 60 minutes to produce an item and your Takt time is 6 minutes, this means that your line should ideally have 10 production steps to keep up with the pace.
Managing Production Peaks
As we know, demand is never constant. It is essential to anticipate production peaks. For example, if your demand increases by 30% at a certain time, you must be able to absorb this surplus. This may involve mobilizing more people, adding machines, or reorganizing your line to maintain productivity.
Analyzing production peaks and troughs also allows you to plan for the flexibility of your line. You may consider adjusting work schedules or introducing continuous improvement periods during off-peak times, further reducing waste on the line.
Reducing Waste
One area for improvement during balancing is to reduce waste (red times). Imagine you manage to reduce production time from 60 minutes to 40 minutes by eliminating 20 minutes of waste. Your line will then be faster, more efficient, and you may even be able to reduce the number of steps.
Reducing red times is possible by analyzing the causes of waste, for example, through methods like the 5 Whys or the Ishikawa diagram. This helps identify inefficiencies that can be corrected, allowing you to better balance your line.
Conclusion: Balancing is a Collective Effort
In conclusion, balancing a production line relies on several factors:
- Mastery of Takt time
- Understanding production times
- Reducing waste
It is an iterative process that requires precision and often the involvement of the entire team to achieve maximum efficiency.
If you have any questions or would like to know more about Lean tools, please do not hesitate to contact us. I would be happy to guide you through this process.
NOS ARTICLES SUR LA PERFORMANCE
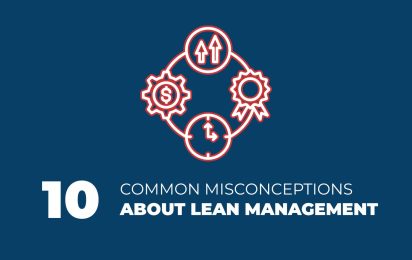
10 Common misconceptions about lean management
10 Common misconceptions about lean management Lean Management- sound familiar? This organizational approach, renowned for transforming companies into well-oiled machines,…
Lire l’article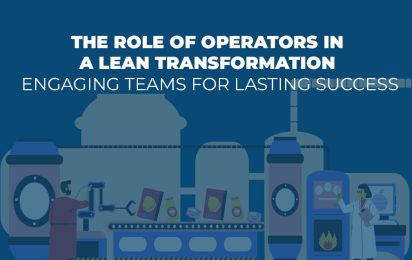
The Role of Operators in a Lean Transformation: Engaging Teams for Lasting Success
How can businesses stay competitive in an ever-evolving world? How can they eliminate waste while creating more value every day?…
Lire l’article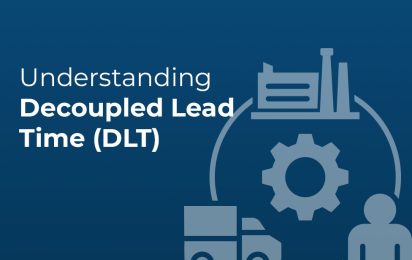
Decoupled Lead Time (DLT): Understanding and Optimizing Lead Time in Supply Chains
In a context where responsiveness and flexibility have become essential, companies are constantly seeking to optimize their supply chains. Among…
Lire l’article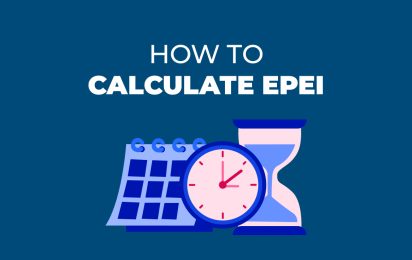
What is EPEI and how to calculate it?
In the world of Lean manufacturing and industrial process management, Every Part Every Interval (EPEI) is a fundamental concept for…
Lire l’article