What is EPEI and how to calculate it?
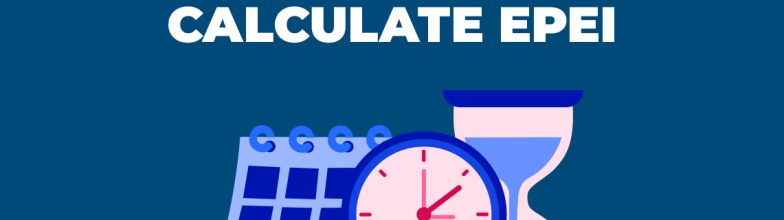
In the world of Lean manufacturing and industrial process management, Every Part Every Interval (EPEI) is a fundamental concept for ensuring efficient and balanced production. It’s a production strategy that aims to produce each part or product at regular intervals, thus optimizing resource utilization and minimizing waste – core principles of Lean!
Understanding EPEI: Definition and Objective
EPEI is a key indicator used in pull production systems, particularly in high-mix, low-volume production environments. It involves determining the frequency at which each product should be manufactured in a given period to meet customer demand while minimizing inventory and wait times. The primary goal of EPEI is to create a production rhythm that is regular and predictable. This helps balance the workload, reduce production cycles, and optimize the use of machinery and personnel. By applying this principle, companies can better respond to fluctuating demand while avoiding excess inventory or shortages.
How to Calculate EPEI?
Calculating EPEI is relatively simple but requires a good understanding of demand and production capacity. The basic formula is:
EPEI = Available Time / Quantity to Produce
Available time is the effective production time, usually measured in hours or minutes per day, week, or month. The quantity to produce corresponds to the total number of units of each product type you need to manufacture in that timeframe. For example, if you have 480 minutes available in a workday and you need to produce 6 different product types in equal quantities, the EPEI would be 80 minutes (480 minutes / 6 products). This means each product should be produced every 80 minutes to maintain a steady flow.
Benefits of EPEI
Implementing EPEI offers several advantages in a Lean environment:
- Reduced inventory: By producing each product at regular intervals, you reduce the need to hold high levels of inventory, lowering associated costs and the risk of obsolescence.
- Improved flexibility: A well-designed EPEI system allows for quick reactions to changes in demand, as production is already planned to be regular and adaptable.
- Process stabilization: EPEI helps standardize production processes, making it easier to identify and resolve issues, and continuously improve production efficiency.
- Reduced changeover times (SMED): By producing each product regularly, you’re incentivized to reduce tool and machine changeover times, a key objective of SMED (Single Minute Exchange of Die).
Challenges of EPEI
While EPEI is a powerful tool, its implementation is not without challenges:
- Demand variability: In environments with highly fluctuating demand, maintaining a constant EPEI can be difficult without frequent adjustments.
- Production capacity: If production capacities are not sufficiently flexible or changeover times are too long, EPEI can become difficult to adhere to.
- Planning complexity: Planning an EPEI for a wide variety of products can be complex, especially if production cycles vary greatly from one product to another.
To conclude
EPEI is a fundamental concept in Lean Manufacturing, particularly for companies seeking to improve their responsiveness while maintaining low inventory levels. By determining the optimal frequency at which each product should be manufactured, EPEI helps balance production, reduce waste, and better meet customer demand. However, implementing EPEI requires a good understanding of production capacities, rigorous planning, and a strong commitment to continuous improvement. With these elements in place, EPEI can transform how a company manages its production, offering a significant competitive advantage in a demanding market.
Our last posts
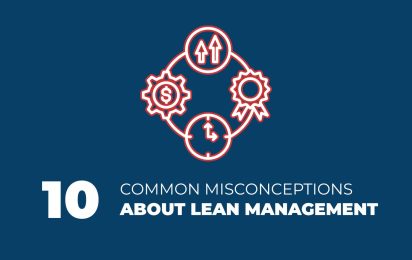
10 Common misconceptions about lean management
10 Common misconceptions about lean management Lean Management- sound familiar? This organizational approach, renowned for transforming companies into well-oiled machines,…
Lire l’article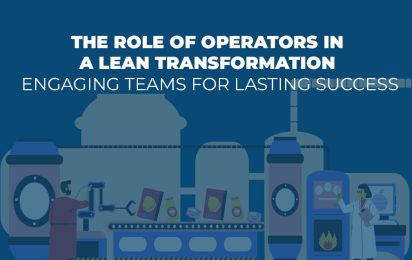
The Role of Operators in a Lean Transformation: Engaging Teams for Lasting Success
How can businesses stay competitive in an ever-evolving world? How can they eliminate waste while creating more value every day?…
Lire l’article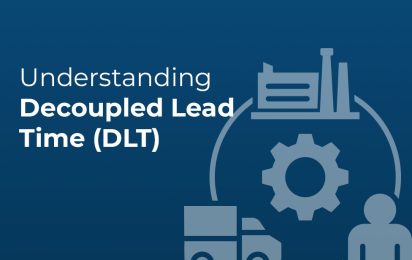
Decoupled Lead Time (DLT): Understanding and Optimizing Lead Time in Supply Chains
In a context where responsiveness and flexibility have become essential, companies are constantly seeking to optimize their supply chains. Among…
Lire l’article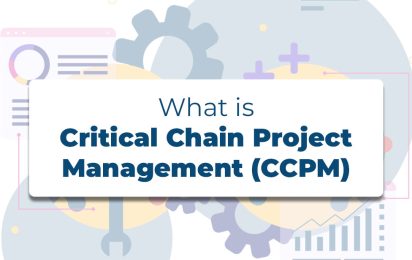
Critical Chain Project Management (CCPM)
In this article, we will explain how to balance a production line to optimally meet customer demand. You will find…
Lire l’article